
Most twist-on wire connections are largely dependent upon installer skill and, as such, remain inconsistently reliable. However, with advantages came disadvantages. Twist-on wire connectors saved installation time, required less operational space, and reduced costs. The wires were initially encapsulated in ceramic and later in plastic.

This would ultimately lead to a connector that you could twist together with your fingers. Eventually, he developed a connection in which the wires were twisted together with a screw. As an electrical contractor, he had suffered injuries from molten solder and was looking for a low-risk way to connect wires. When Marr developed the twist-on wire connection, he was looking for a faster and safer way to make electrical connections. If you open junction boxes in many homes, you will see a plethora of colorful connectors with multiple wires feeding a number of different electrical applications. In order to reduce installation time and make it easier to fit connections into smaller spaces, the twist-on wire connector was born. Many countries have mandated a shift to lead-free or composite solder made of lead and tin, which has made some connections weaker.
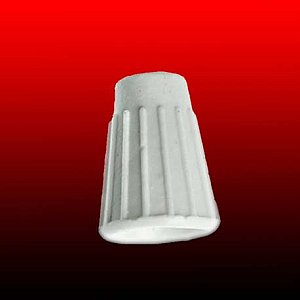
Soldering by hand is a time-consuming and inexact science and there are hazards associated with using molten metal and lead-based solder. Some solders are not able to be used in high-temperature situations and the strength of the joints often remains low, even when the joint is additionally held together by adhesives. The inherent variability of workplace environments, temperature fluctuation, material quality, and user skill can negatively impact the consistency of the process. It is also a process that has become automated.Įven though soldering has been around for centuries, it still has drawbacks. For instance, soldering provides a low-process solution to connect wires. These older wire-splicing connection methods have not disappeared completely, however, as they still offer advantages. While you still may see a screw connection or twist-on wire connector in a junction box, lever or push-in connectors have become the norm. The connectors used with these wires have changed quite a bit as well. In addition, wires are now generally coated with a non-metallic sheathing made primarily of plastic. Today, flexible metal conduits are still used, although PVC conduits may be more applicable in harsh-environment application areas. This connection method, also known as wire nut connectors, was the norm until recently, when companies introduced more reliable connection methods, such as lever or push-in connectors.

The newest connection, the twist-on wire connector, was introduced in the United States around 1933 by electrical contractor William Marr. This conduit could travel through wood and metal framing as well as exposed areas without exposing people to live wires. The metal conduit allowed a grouping of wires to be pulled through a metal tube, which could also double as a grounding method. The rubber fabric allowed both hot and neutral wires to run together, but there was still no ground wire. Just ahead of World War II, the cable and wire industry took a huge leap forward with the advent of rubber-fabric-coated wire sheathing, metal conduit, and a new type of wire connector. Early electrical connection methods are still found in many older buildings.
